Case Releases:
1.0 In general IoT Decision Framework
2.0 Integration of Spare Part Logistics
3.0 Digital Twin Model, AWS
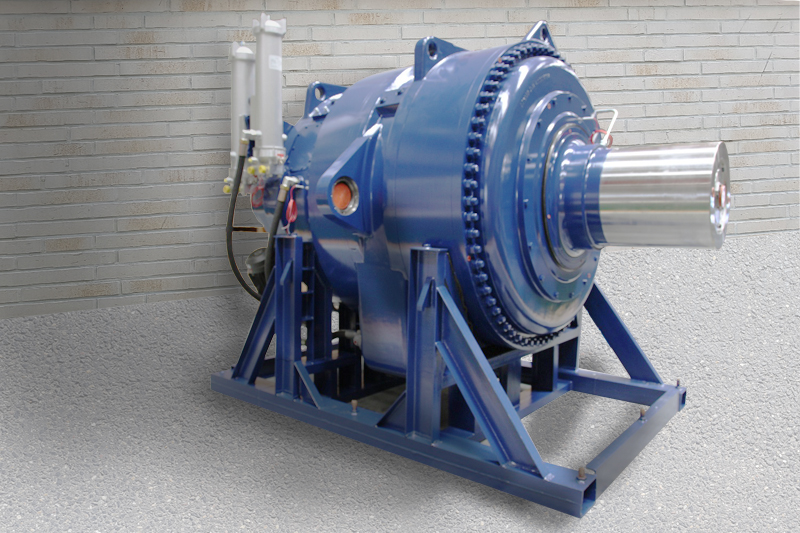
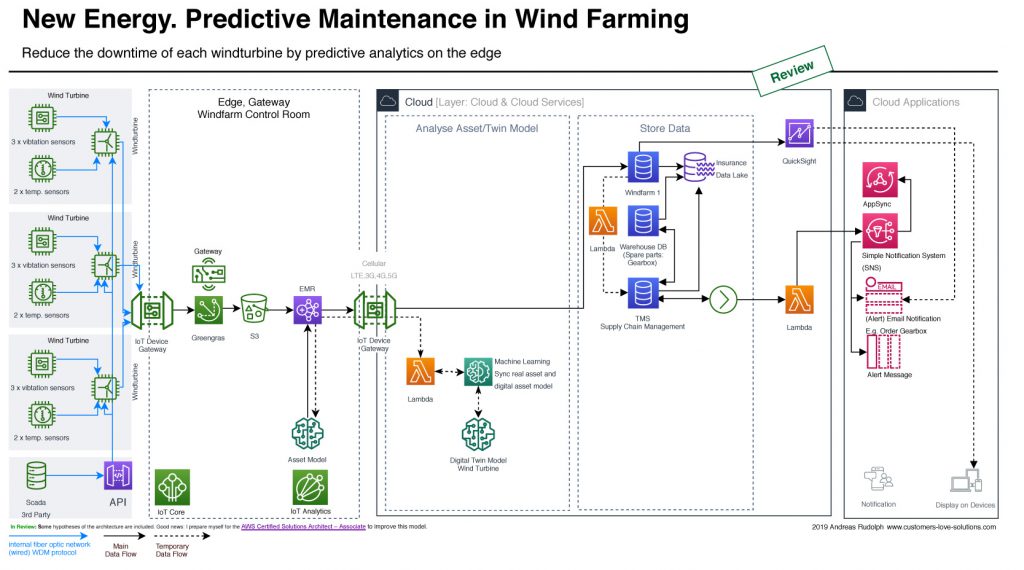
#Intro |
This new energy topic for spare part logistics for wind turbine now is in iteration 3. That means getting further insights, I improve the case further on to learn and optimize the solution. I started with the case of Daniel. But in touch with New Energy Industry, I interviewed different users. E.g. „Momme“, a manager of EON New Energy Solution I met and also Peter, a technician for wind turbines shared his insides about major challenges of maintenance in his job. So it gets personal, this is essential to understand,who is the user, what is the most relevant requirement? To build the bridge from the level of case study I researched as well the supply chain of spare part logistics. And to tackle the concept of Digital Twins I learned about this topic quite a lot and embedded it in my AWS architecture in the technology area, but improvement is still in progress! |
# Problem Statement |
Most wind farms and it’s several hundreds wind turbines are very often located in remote areas. Onshore over a wide area of hundreds of square kilometers is common, but offshore as well. Europe is leader in offshore wind energy. The main challenge happens, if a critical part of a wind turbine breaks, it takes several days till a spare part like the gearbox could be delivered in remote areas without transport network with a lack of coverage of connectivity for smart wind turbines in case of an alert message. https://en.wikipedia.org/wiki/Wind_farm |
#Value Proposition “the Solution” |
As a logistic company partner with an industrial software company specialized on predictive analytics for wind turbine maintenance to reduce the Downtime till fixing. The solution provides the spare part order and informs the technician about the urgent needed maintainance synchronized with the arrival of the delivery of the spare part. |
#Product |
Spare part logistic for Smart Wind Turbine, especially for the gearboxes, the most critical part. |
#MVP / Release Goal |
Roll out a system to predict maintenance including an autonomous spare part supply chain for smart wind farms in remote areas. Reduce downtime up to -70% of time from usually ~4 weeks. |
#Target Costumers / Sector Industries |
Smart Wind farm owners and New Energy companies. |
#Size of Target companies |
Large wind farms > 100+turbines are minimum. |
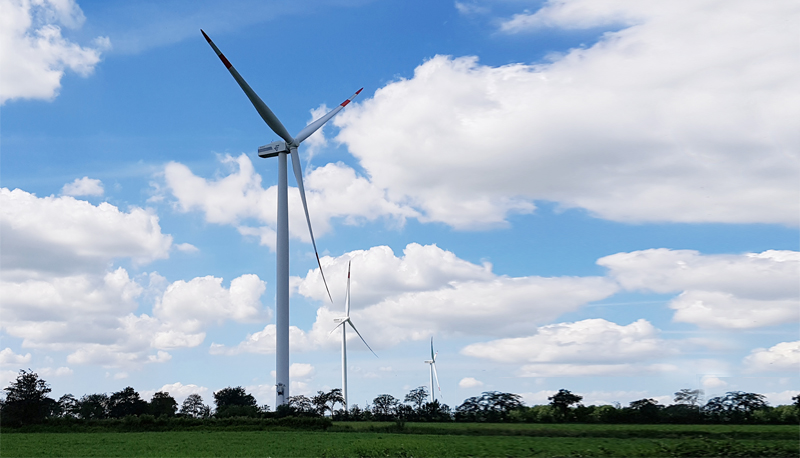
#Summary & Key learnings |
This case was great to get explore the IoT decision framework from Daniel Elizalde, part of the online course. But also to understand how the share part logistic for wind farm industry is changing the new energy market for logistics. The information of the urgent need of a spare part is included in a SaaS solution with an predefined order towards a connected carrier, who gets the shipment data much earlier than in analog times. Some links: https://www.decisyon.com/case-study-with-optimized-operations-smart-wind-farms-can-weather-any-downtime/ https://www.iwes.fraunhofer.de/en/research-projects/finished-projects-2019/smart-wind-farms.html https://www.energy.gov/sites/prod/files/smart_wind_turbine_data.pdf https://www.siemensgamesa.com/explore/innovations/digitalization |
The IoT Decision Framework:
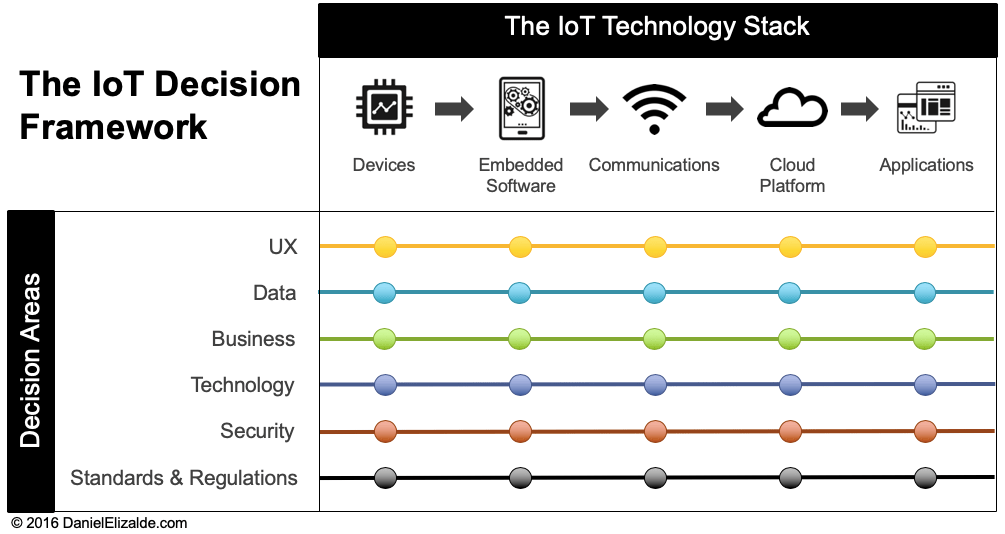
If you would like to learn more about the framework, click here: https://danielelizalde.com/iot-decision-framework/
UX: |
This area is about identification of different user and roles using the solution. That means for their activities, there is a different usage, therefore are maybe other features required. Core questions to answer are: – Who is the Customer? Who the User? – What is the key value for each of them? – What is in essential for MVP vs. Backlog and Roadmap? – Do we have different user groups? Customers, extern vs. intern partners? Describe your personas as clear as possible to help all team members you need to build this solution. External User Group: —————————————————- 1. Peter Petersen, 33 y., Wind Turbine Service Technician, [primary customer persona], ext. Customer Activities/Responsibilities: 1.1. monitoring and service management for wind farm health. 1.2. Schedule + manage maintenance 1.3. Quartly report of health status of wind farm (incl. historical reports, e.g. turbines offline with service, scheduled maintenance whithin next 6-12 months) —————————————————- 2. Mike Maker, 55 y., Wind Farm Owner, ext. Customer Activitities/Responsibilities: 2.1. Evaluate vendors (Responsible for ROI of the business) 2.2. Review quarterly reports —————————————————- 3. Tim Tech, 35y., Installation Technician, ext. Partner 3.1 Install/uninstall edge device 3.2 Performance maintenance on the turbine 3. —————————————————- Internal User Group: 4. Carol Controltower, 27 y., Operations Engineer, int. User Activities/Responsibilities: 4.1. Handle provisioning and decommissioning 4.2. Monitor health of each wind farm 4.3 Schedule and manage maintenance + Spare part order 4.4 Keep edge software up-dated on device monitoring —————————————————- 5. Sonja Salesforce, 32 y., Sales Representative, int. User Activities/Responsibilities: 5.1. Demo the capabilities of our solution —————————————————- 6. Wayne Warehouse-Wizard, 52 y., Transport Manager & Warehousemanager, int. Network Partner Smart Carrier Activities/Responsibilities: 6.1 Short-term Delivery of gearbox after alert-notification 6.2 Pre-Notification of estimated drop off time to Service Technician 6.3 Spare part management in fulfillment center ================= MVP ================ Prio – Persona – Requirement (Activity) 1 – Peter Petersen -Install the edge device 2 – Carol Controltower -Provision a new turbine 3 – Carol Controltower -Monitor health of a complete farm 4 – Carol Controltower -Generate alerts if turbine needs maintenance 5 – Carol Controltower -Monitor health of single turbine in real-time 6 – Wayne Warehouse-Wizard –Pre-Notification of estimated drop off time for edge devices / e.g. gearbox ================= Backlog ================ Tbd … |
#Business |
The area business is were the rubber hits the road! Good to review your business model. Check, if ROI is given! The area of revenue is divided into one-time and recurring revenue, in the overall layer solution in the stages of customer lifecycle management, CLM are: Install, Provision, Onboard, Operate, Maintain, Decomission. But as well there are revenue opportunities on the level of the IoT Technology Stack: Device, Device Software, Commuications, Cloud Plattform, Cloud Applications. Same logic applies to the cost: One-time and recurring cost at the CLM level and per Technology Stack. |
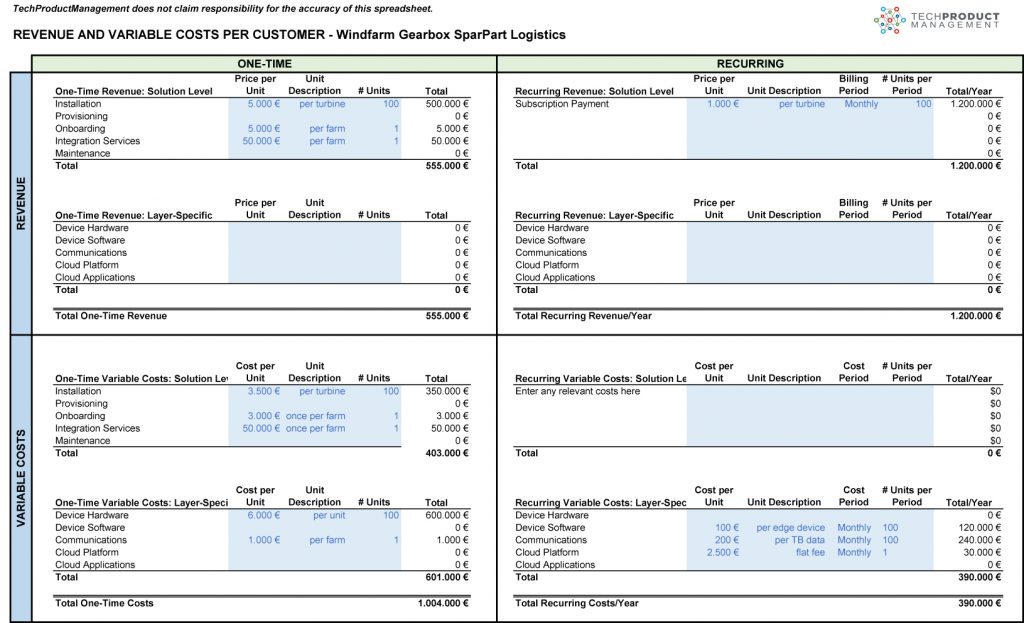
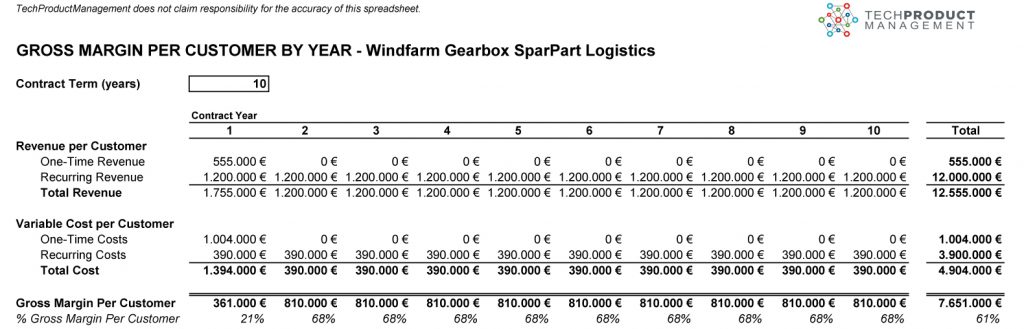
#Data |
From customer’s feedback and shared historical data our team identified the gearbox is the critical spare part. It takes the longest time till fixing is done and cost the most lost energy and revenue for the wind farm owner while downtime for over 4 weeks. The MVP must focus on predictive maintenance of thegearbox. Coming back to data, we ask the engineering team for details. – What status we have to messure? – How much data is produces and needed per device? – When to messure? Real-time on the edge, because it’s a critical decision to make. Feedback: · Temperature · Vibration Feedback of a vendor of temp and vibration sensors topredict gearbox breakdown: Temperature: 5 sensors —————————————— Sensor type: Thermocouples Resolution: 16 bits (2 bytes) Sample rate: Once a minute Vibration: 3 sensors —————————————— Sensor type: Accelerometer Resolution: 24 bits (3 bytes) Sample rate: 50 kHz (50k sample/sec.) Amount of data/year = resolution (in bytes) x sample rate x number of sensors, multiplied up to a year. 60 min x 24h= 1440 min/h 1440 * 365d = 525.600 min/year Temperatur —————————————— Turbine/year: 5*2 bytes/min *525600 min/y = 5.256.000 bytes/y= 5.256 MB/year Wind Farm/year: 5.256 MB/y * 100 wind turbines = 525.6 MB/year Vibration —————————————— Turbine/year: 3 *3 bytes * 50 kHz * 60sec * 525.600 min/y = 14.191 TB/year Wind Farm/year: 1.419,12 TB/y * 100 = 1.419 PB/year Total data per year (temperature + vibration) · Per single turbine = 5.256 MB/year + 14.19 TB/year = 14.191205256 TB/year · Per farm = 525.6 MB/year + 1.419 PB/year = 1.4191205256 PB/year To break it down, in the area of data it’s essential to look e.g. at the required data and the manipulated data per layer. That means on the device hardware level temperature and vibration data are generated, while wind speed, rotation speed, location, installation date and maintenance history is available by the device software. Via API’s at the cloud layer, we aggregate additional weather data, wind speed, simulation models from the manufacturer. By using machine learning we can analyze in the cloud for a better forecast of maintenance of each wind turbine by creating a Digital Twin. |
#Technology |
This architecture model show cases how to manage the connectivity in a remote area to collect data from each sensor per device/wind turbine. By using a gateway not every sensor must have a component for communication to the cloud. In this case is existing device software (Scada) in the smart wind turbine already available. So don’t re-invent the wheel, connect to existing infrastructure and use the internal fiber optic network [wired] to transport sensor data to the gateway. To analyse nearly real-time we need analytics at the edge. Comparing real maintenance data of each wind turbine with the asset model is used to find anomalies. If the alert-level of the expected data is achieved, the alert process to the supply chain team of the carrier (Transport Manager & Warehousemanager) will be triggered and also the scheduling of the Wind Turbine Service Technician. At the cloud in a definite periode of time an alignment of the asset model and the digital twin model happens. The target is to have always current data at the edge for the asset model. |
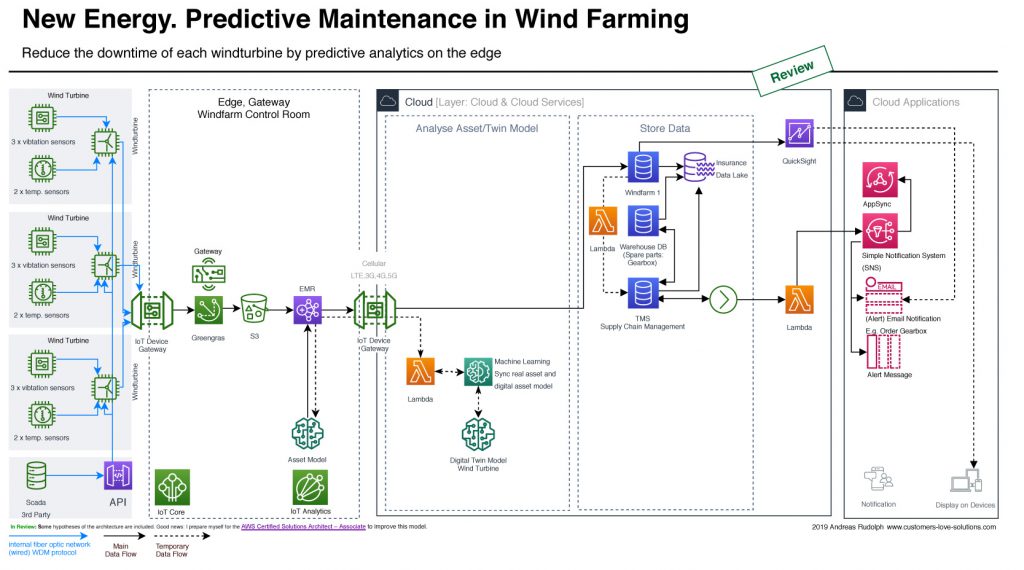
#Security |
Security is a topic from the very first beginning for real world security as well as for cyber security at all layers of your solution. Priority – Security Challenge – Mitigation Plan – Impersonation during OTA update – Integrate a 3rd party OTA solution into our product – Connecting unauthorized devices into the communication ports – Enclose the device hardware in a locked, shocked resistant box – Take over the OS during reboot – Implement anomaly detection in real-time in the device software |
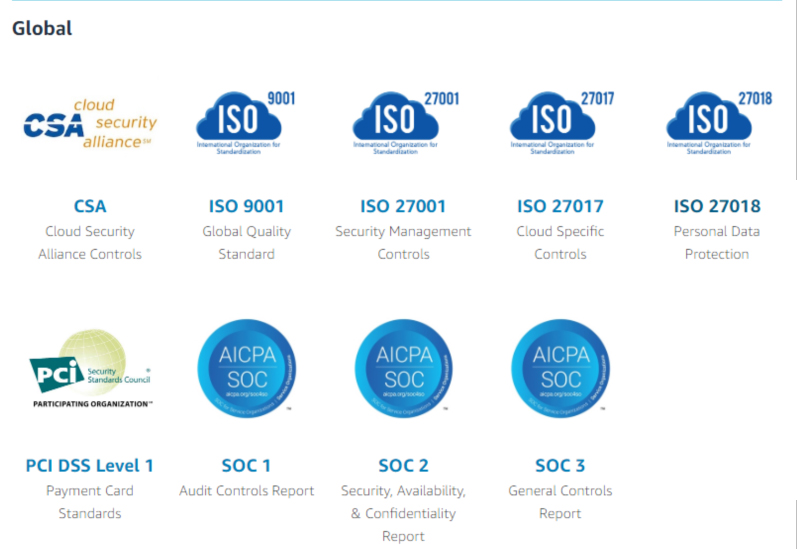
#Standards & Regulations |
It’s always relevant to know the standards & regulations specific for your industry, the country or maybe your company, before first roll out. These are only same examples to get an idea what kind of regulations you should think about. |
Device | – UL – FCC – Fire department |
Device Software | – Interconnection regulation – Back-feeding regulation |
Communications | – FCC |
Cloud Platform | – NIST and NERC CIP security standards |
Cloud Applications | – N/A |